Indice
In siderurgia il ruolo di MO è svolto dagli ossidi di ferro, la cui serie, in funzione del tenore di ossigeno calante, è la seguente:
Fe2O3 → Fe3O4 → FeO —— Fe
e, partendo da Fe2O3, la riduzione con CO segue la stessa sequenza. Le reazioni coinvolte sono le seguenti:
3Fe2O3 + CO ↔ 2Fe3O4 + CO2 (6)
Fe3O4 + CO ↔ 3FeO + CO2 (7)
FeO + CO ↔ Fe + CO2 (8)
A bassa temperatura è possibile anche la reazione:
Fe3O4 + 4CO ↔ 3Fe + 4CO2 (9)
In coordinate di Boudouard le curve di riduzione degli ossidi di ferro generano la figura dove i numeri corrispondono alle reazioni.
Si nota che la curva di riduzione di Fe2O3 per temperature al di sotto di circa 1200 °C coincide con l’ordinata di Boudouard a 0% di CO, indicando che bastano tracce di CO nella fase gassosa per attivare la reazione (6). Ne risulta che Fe2O3 è un ossido facilmente riducibile con CO, ed in modo analogo si comportano alcuni altri ossidi non ferrosi come Cu2O (ossido rameoso) , PbO (monossido di piombo), NiO (ossido di Nichel). Gli altri ossidi di ferro sono riducibili soltanto in presenza di una adeguata quantità di CO nella fase gassosa. Esistono anche ossidi, come MnO (monossido di manganese) e SiO2 (diossido di silicio) , la cui curva di riduzione coincide con l’ordinata al 100% di CO: questi non sono riducibili con CO.
Usando la convenzione indicata in precedenza, in figura sono indicati i campi di stabilità degli ossidi di ferro e quello del metallo Fe. Inoltre è stata sovrapposta la curva di Boudouard.
L’esame della figura risulta molto esaustivo. Supponiamo che a 800 °C il sistema sia costituito da Fe2O3, C e CO2, senza presenza di CO (punto A). Immediatamente si attiva la reazione di Boudouard nel verso della formazione di CO (reazione 3’), ma il CO prodotto viene subito utilizzato da Fe2O3 per ridursi a Fe3O4 (reazione 6). Soltanto a completo esaurimento di Fe2O3 diventa possibile l’incremento della quantità di CO nell’atmosfera gassosa. Quando viene raggiunta la composizione corrispondente all’ascissa del punto B si attiva la reazione 7 e l’ossido Fe3O4 si riduce a FeO. Completata la riduzione a FeO, la quantità di CO nella fase gassosa può crescere fino al valore dell’ascissa del punto C, in corrispondenza del quale si ha la riduzione di FeO a Fe metallico (reazione 8). Completata la riduzione, la presenza di una ulteriore quantità di C fa sì che la reazione 3’ possa continuare a generare CO fino al raggiungimento della composizione di equilibrio corrispondente al punto D.
Aspetti pratici della riduzione degli ossidi di ferro
Quanto sopra è la chimica della riduzione degli ossidi di ferro, cioè teoria. A questo punto si può tentare di fare un primo passo per passare dalla teoria (relativamente semplice) alla realtà (molto più complicata). La pratica attuale prevede che la riduzione degli ossidi di ferro avvenga in un reattore chiamato altoforno: la parola stessa induce a pensare alla maestosità di tale reattore, che in casi particolari, sommando anche le strutture accessorie, può raggiungere altezze superiori a 60 m. Schematicamente, l’altoforno è costituito da due tronchi di cono dissimili a base sovrapposta (Fig. 10).
Convenzionalmente la parte alta dell’altoforno si chiama bocca: da lì vengono caricate le materie prime e gli additivi, e da lì escono i gas esausti. Il tronco di cono è il tino (quindi c’è un tino superiore ed uno inferiore), mentre la zona di giunzione fra i tini si chiama ventre. Sul tino inferiore si innesta il piano degli ugelli, attraverso i quali si immette aria o, più modernamente, aria arricchita con ossigeno prodotto da distillazione dell’aria: si limita così l’effetto svolto dall’azoto, negativo sia dal punto di vista termico (assorbe calore senza avere una funzione nel processo) sia sulla qualità del prodotto finale (tranne in alcuni casi particolari viene considerato un inquinante dell’acciaio). Il reattore termina con il crogiolo, entro cui si raccolgono due fasi liquide immiscibili, il bagno e la scoria, che devono essere spillate separatamente.
Di seguito riporto alcune informazioni sull’altoforno, senza alcuna pretesa di completezza. L’altoforno è una struttura d’acciaio rivestita internamente da mattoni di refrattario inseriti ad incastro (tipo LEGO, con il minimo di chiodatura con la struttura metallica). Nelle industrie siderurgiche è attiva una batteria costituita da almeno tre altoforni: operativamente, mentre uno è in fase di caricamento, nel secondo avviene la riduzione, ed il terzo è in manutenzione (di solito per la sostituzione di mattoni di refrattario danneggiati). Alcuni studi datati, ma considerati ancora validi, hanno mostrato che la produttività non aumenta se l’altezza dell’altoforno è maggiore di 30 m (valore che viene pertanto considerato il limite pratico), mentre dipende molto dal diametro massimo, nella zona del ventre, ove però è assai difficile intervenire praticamente. Si ricorda che poichè l’azione riducente è garantita da un flusso gassoso ascensionale, non è necessaria la miscelazione preventiva delle materie prime, le quali sono introdotte nell’altoforno a strati.
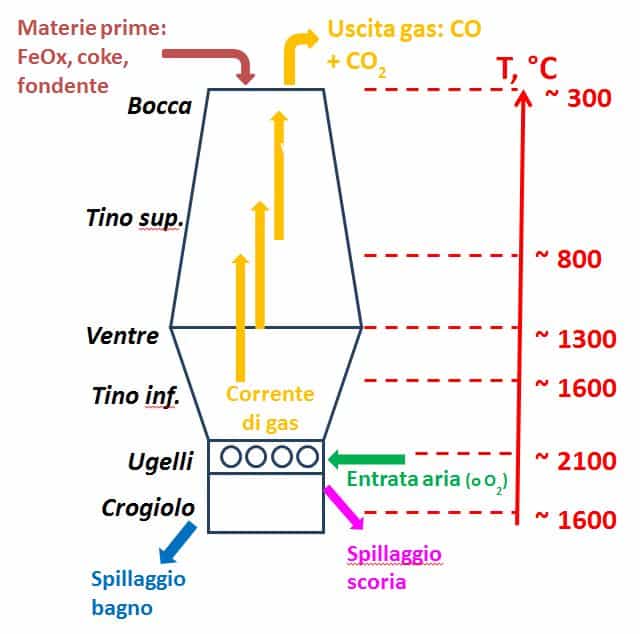
Oltre ai minerali ferrosi e al coke si immette calcare (CaCO3) o calce (CaO), prodotti che svolgono una serie di funzioni importanti nella chimica dell’altoforno tra cui la promozione della fase liquida (da cui il titolo generico di “fondente”). La bocca è la parte più fredda del reattore ed è anche una delle zone più critiche di tutto il sistema. In particolare in prossimità della bocca si raccoglie il carbonio piroforico, prodotto nei processi di riduzione indiretta: si tratta di un prodotto pulverulento ed assai reattivo tanto che per evitare incendi e scoppi è necessario impedirne il contatto con l’aria.
Ciò ha reso necessaria la messa a punto di strumentazioni particolari per il caricamento delle materie prime. In siderurgia non si può sprecare energia e poiché i gas esausti escono caldi dall’altoforno, il loro calore viene recuperato nelle torri cowper, che sono strutture contenenti mattoni di refrattario che vengono scaldati dai gas: invertendo il flusso gassoso, i mattoni caldi servono per preriscaldare l’aria (o l’ossigeno) che verrà introdotta al piano degli ugelli. Scendendo dalla bocca fino al crogiolo la temperatura all’interno dell’altoforno aumenta continuamente: i valori riportati in Fig. 10 sono soltanto indicativi, anche se in passato sono state fatte alcune valutazioni sperimentali, difficili e poco precise (una precisione maggiore è stata ottenuta con i moderni metodi simulativi). Scendendo nell’altoforno, la carica subisce sia fenomeni fisici (dapprima essiccamento, poi, quando la temperatura raggiunge circa 1300 °C, inizio fusione che si completa a temperature maggiori) sia effetti chimici (riduzione diretta e indiretta). La temperatura più elevata, con valori superiori a 2000 °C, si riscontra al piano degli ugelli che è un altro punto critico dell’altoforno. Se si considera l’altoforno come un reattore ove avvengono reazioni di riduzioni, a livello degli ugelli l’ambiente è ossidante! Perché? Per spiegarlo è necessaria qualche informazione preventiva.
Nell’altoforno al piano degli ugelli arriva una carica che, in prima approssimazione, si può considerare costituita da ferro liquido in cui, convenzionalmente, si assume che il carbonio sia completamente solubile (in realtà non è vero, ma questo aspetto è di importanza più teorica che pratica). Attraverso gli ugelli si immette nell’altoforno un flusso gassoso contenente molto ossigeno il quale reagisce col carbonio secondo la reazione (1) generando un ambiente ossidante, con molto CO2. La carica liquida, risultato di precedenti reazioni di riduzione, incontrando tale ambiente si riossida con una perdita netta del risultato che si vuole ottenere.
Nelle condizioni reali, calcoli sperimentali hanno mostrato che la zona ossidante è un volume in prima approssimazione semisferico, con al centro l’ugello e di raggio pari a circa un metro: quindi se il diametro al piano degli ugelli fosse due metri tutta la carica sarebbe interessata alla riossidazione. Per ridurre l’effetto si è reso necessario aumentare il diametro al piano degli ugelli fino a 8-10 m, fatto che ha indotto notevoli complicazioni strutturali. Quando arriva nel crogiolo, la carica si ripartisce in due liquidi immiscibili: per ragioni di densità si pone al di sotto il “bagno” costituito da ferro liquido con carbonio disciolto contenente anche elementi chimici come Si, Mn, P e altri che, presenti nella materia prima in forma di ossidi (SiO2, MnO2, o 3CaO.P2O5,….), hanno subito reazioni di riduzione da carbonio. Al di sopra si pone la “scoria” (detta anche “loppa”) costituita da quanto di non ferroso e non metallico c’è nel sistema, materiale in gran parte derivante da inerte presente nella materia prima con l’aggiunta dei prodotti di reazioni chimiche che vengono attivate allo scopo di depurare il bagno da elementi inquinanti (è il caso dello zolfo che accompagna il coke). Poiché se ne produce circa una tonnellata per tre tonnellate di bagno, cosa farsene della loppa è sempre stato un problema per l’industria siderurgica!
La presenza di una certa “idraulicità” ha indirizzato la loppa verso l’impiego come cemento, anche se quello “di scoria” è il prodotto di minor qualità in questo campo. Una piccola parte viene trasformata in “lana di scoria”, ottenuta per insufflamento di aria nel liquido, da usare per fabbricare pannelli termo- e fonoassorbenti. Comunque ne rimane una grande quantità che viene discaricata (sulla carta non è un “rifiuto pericoloso”) o utilizzata come materiale di riporto per manto stradale o simili. (In Italia quest’ultimo tipo di impiego è ora proibito per problemi ecologici. In passato non era così: non posso verificarne la veridicità, ma si dice che le piste di atterraggio a mare dell’aereoporto di Genova siano state costruite sulle loppe della allora Italsider!). Modernamente sono state attivate soluzioni per diminuire da quantità di scoria: si è ricorsi alla “preriduzione del minerale” nel sito di estrazione, ottenendo minerale arricchito con ovvi vantaggi anche per quanto riguarda la fase di trasporto verso l’impianto siderurgico.
Tornando ad aspetti meno pratici si ribadisce che in siderurgia deve essere attivato qualsiasi artificio atto a consentire un risparmio energetico: qui svolge un ruolo fondamentale la termochimica delle reazioni di riduzione.
Termochimica siderurgica
Ho sempre avuto una certa simpatia per quelle cose che si chiamano “funzioni di stato”. Non mi ricordo chi e in quale occasione mi presentò il concetto di “funzione di stato”, ma mi circola ancora nella mente la similitudine utilizzata. “Avete presente una montagna, ad esempio il Monte Bianco? Se siete in grado di salire in cima, potete scegliere di farlo percorrendo la via francese, o quella italiana che sono le vie normali, o forse una di quelle vie non normali. Al limite potreste anche salire in elicottero. Bene: in qualunque modo voi arriviate in cima al monte Bianco sarete sempre a 4810 metri sul livello del mare! Cioè non importa come lo avete raggiunto ma il risultato finale è sempre lo stesso!”. Semplice, come non averci pensato? Certamente c’è qualche sottinteso che bisogna evidenziare: nel caso dell’altezza dei monti il concetto vale se si prende come riferimento il mare e si dice che la sua altezza vale 0. Quindi una funzione di stato è una entità la cui variazione per passare da uno stato iniziale A a uno stato finale B è sempre la stessa, qualunque sia la via percorsa per andare da A a B.
In chimica le funzioni di stato svolgono un ruolo fondamentale, sopratutto in quella branca nota come “chimica fisica”. In termochimica la funzione di stato fondamentale si chiama “calore (o entalpia) di reazione”, entità che quantifica l’effetto termico associato ad una reazione. Nel 1840, (cioè prima che fosse dedotto il concetto di conservazione dell’energia), Germain Henry Hess (Fig. 11) pubblicò la legge che porta il suo nome, secondo la quale se in un sistema chimico ci sono dei reagenti che generano dei prodotti, l’effetto termico globale (a pressione costante) è lo stesso qualunque sia la successione degli stadi di reazione che hanno portato dai reagenti iniziali ai prodotti finali. Cioè il calore di reazione è una funzione di stato. Anche in questo caso è necessario stabilire dei riferimenti: la pressione nel sistema chimico deve essere costante, e per fare calcoli deve essere noto il “calore (o entalpia) di formazione” di ciascuna specie reagente e di ciascun prodotto finale, con la convenzione che per gli elementi chimici puri il suo valore è 0 Kcal o KJ (si ricorda che: 1 Kcal = 4,184 KJ; 1KJ = 0,239 Kcal).
Un esempio che ha riflessi fondamentali in siderurgia è il seguente. Nell’altoforno si raggiungono elevate temperature a seguito della combustione del coke (cioè C) con l’ossigeno secondo la seguente reazione:
C + O2 → CO2 – 94,1 Kcal
Cioè una mole di C reagisce con una mole di O2 producendo una mole di CO2 e sviluppando 94,1 Kcal.
Si noti che la reazione, essendo una combustione, è esotermica cioè sviluppa una quantità di calore che è valutabile sperimentalmente: la convenzione termodinamica esprime questo effetto attraverso il segno meno; le reazioni che assorbono calore sono endotermiche ed hanno il segno più.
Si possono giustificare questi segni considerando la reazione chimica come un sistema chiuso, che può scambiare con l’ambiente solo energia (non materia): visto dal sistema, lo sviluppo di calore nell’ambiente porta ad una diminuzione del suo contenuto energetico; contrario, l’acquisizione di calore dall’ambiente significa un incremento di energia. La combustione di C con O2 passa attraverso lo stadio intermedio di formazione di CO che poi si trasforma in CO2. Le reazioni coinvolte nei singoli stadi con i relativi effetti termici sono le seguenti
2 C + O2 → 2CO – 52,8 Kcal
2 CO + O2 → 2 CO2 – 135.4 Kcal
la cui somma definisce la reazione totale e la somma degli effetti termici è la conferma della legge di Hess.
2 C + 2 O2 → 2CO2 – 188,2 Kcal
Anche la reazione di Boudouard è esotermica in una direzione:
2CO → C + CO2 – 41 Kcal
Ovviamente ciò che è eso in una direzione diventa endo in direzione opposta, per cui:
C + CO2 → 2CO + 41 Kcal
Sono reperibili numerose tabelle che raggruppano i valori del calore di formazione di composti chimici, alcune anche molto complete: si evidenzia che a seconda delle fonti lo stesso composto può avere valori leggermente diversi, e su ciò influisce la data della tabella poichè moderni metodi di valutazione sono sempre più precisi.
Quanto sopra ha riflessi fondamentali nella produzione dell’acciaio. Nell’altoforno, per poter ridurre la carica costituita da ossidi di ferro e da coke, si deve generare una atmosfera gassosa la cui composizione media segue la curva A-B in figura, che è sempre entro il campo di stabilità di Fe e si posiziona sopra (quadrante II) o sotto (quadrante IV) della curva di Boudouard. L’altoforno viene caricato dall’alto, quindi la carica incontra dapprima le condizioni presenti nel IV quadrante, dove l’atmosfera gassosa è ricca in CO la cui percentuale deve diminuire per tendere all’equilibrio. Le reazioni possibili sono le seguenti
3Fe2O3 + CO → 2Fe3O4 + CO2 – 16.2 Kcal
Fe3O4 + CO → 3FeO + CO2 + 3.1 Kcal
FeO + CO → Fe + CO2 – 4.4 Kcal
2CO → C + CO2 – 41 Kcal
FeO + CO → Fe + CO2 – 4.4 Kcal
che sommata alla reazione di Boudouard fornisce la reazione finale
FeO + C → Fe + CO ¬+ 16.1 Kcal
E’ evidente che dal punto di vista termico conviene raggiungere il quadrante II con la maggior quantità possibile di FeO la cui riduzione a Fe è leggermente eso.
Cosa si produce nell’altoforno
Quanto sopra è un buon esempio di uso industriale di concetti chimici, per cui parrebbe possibile produrre ferro partendo da opportuni reagenti ed applicando correttamente le regole della termodinamica. Ma, come si è già detto, fra teoria e pratica c’è una grande differenza. Innanzi tutto i reagenti non sono ossidi di ferro e carbonio puri, e tutto quanto entra nell’altoforno svolge un qualche ruolo nella chimica del sistema influenzando il risultato finale quasi sempre negativamente, raramente in modo positivo. Di seguito si analizzano i casi più importanti, naturalmente senza pretesa di completezza.
a) Siamo ottimisti e quindi vediamo dapprima un caso di relativa positività. Poiché i loro ossidi sono isomorfi (cioè hanno reticoli cristallini simili), in natura gli ossidi di manganese accompagnano quasi sempre quelli di ferro e quindi fanno parte della carica dell’altoforno. Se nell’altoforno si producesse Mn metallico e questo rientrasse nella composizione del prodotto finale, si avrebbero influenze positive sulle sue caratteristiche meccaniche: per questo si vorrebbe la riduzione quantitativa degli ossidi di manganese presenti nella carica. Probabilmente l’ossido presente è MnO2, biossido di manganese (pirolusite) e la sua riduzione avviene a stadi, di cui il primo è:
MnO2 ¬+ CO → MnO + CO2 – 40.7 Kcal (10)
reazione esotermica che può avvenire nella zona dell’altoforno dove vi è bassa temperatura. La successiva riduzione con CO di MnO a Mn metallico è fortemente endotermica, e potrebbe avvenire solo a temperature molto elevate e al di sopra della curva di Boudouard, cioè nel campo dove è favorita la produzione di CO piuttosto che il suo impiego come riducente. Quindi il Mn metallico si può ottenere solo per riduzione con C (una vera reazione di riduzione diretta) secondo la:
MnO + C → Mn + CO + 69.5 Kcal (11)
reazione fortemente endotermica che può avvenire solo dove più alta è la temperatura, cioè in prossimità del piano degli ugelli dell’altoforno. Risultato: la riduzione non è mai completa e la resa è di circa il 70% rispetto alla quantità iniziale.
b) Uno dei costituenti principali della ganga (ciò che accompagna il minerale fertile) è SiO2, che nell’altoforno potrebbe formare silicati oppure ridursi a silicio metallico. La reazione di riduzione con CO non può avvenire perché, essendo fortemente endotermica, richiederebbe temperature elevate, al di sopra della curva di Boudouard e quindi nel campo di stabilità del CO.
L’unica reazione possibile è quella diretta secondo la:
SiO2 + 2 C → Si + 2 CO + 152 Kcal (12)
che richiede altissime temperature raggiungibili solo nella parte bassa dell’altoforno vicino al piano degli ugelli. La riduzione non è quantitativa, e se si vuole una elevata quantità di Si nel prodotto finale (cosa che produrrebbe un forte incremento del modulo elastico, caratteristica desiderata ad esempio negli acciai per molle), si deve aumentare il coke usato per produrre calore e raggiungere temperature molto elevate (oltre 2100 °C agli ugelli).
c) In molti giacimenti naturali i minerali di ferro sono accompagnati da fosforiti, composti a cui si dà convenzionalmente la formula (CaO)3.P2O5. Sintomatico è il caso delle miniere tedesche e inglesi, ed è proprio l’elevato tenore di fosforo del minerale che ha condizionato lo sviluppo della siderurgia, obbligando a modifiche tecniche fino al raggiungimento dei metodi moderni. Il P è una presenza assai negativa per il prodotto finale, il quale risulta fortemente infragilito.
Si ha notizia di decreti emessi dai reali inglesi del XVI che proibivano l’uso di minerali estratti da certe miniere perché il prodotto ottenibile risultava pericoloso ed inutilizzabile per impieghi strutturali (soprattutto fabbricazione di ponti). In realtà il fosforo è l’unico elemento che nell’altoforno viene ridotto quantitativamente, passando integralmente nel prodotto finale.
Ciò avviene secondo il seguente schema a stadi. Per la inevitabile presenza di silice, dapprima la fosforite si trasforma in silicato liberando P2O5 (anidride fosforica) secondo la reazione:
(CaO)3.P2O5 + 3 SiO2 → 3 CaO.SiO2 + P2O5
P2O5 poi subisce una riduzione diretta a carico di C:
P2O5 + 5 C → 2 P + 5 CO + 236 Kcal (13)
Questa reazione comincia a circa 1100 °C e si completa al di sopra del piano degli ugelli: tutto il fosforo passa nel prodotto finale. Per eliminare il fosforo sarebbe necessario un ambiente basico (che nell’altoforno c’è) e una atmosfera ossidante, impossibile nell’altoforno che è un sistema riducente.
d) Un altro elemento inquinante e fortemente deleterio è lo zolfo che entra nell’altoforno prevalentemente attraverso il coke, talvolta attraverso la materia prima se si usano ceneri di pirite. Fortunatamente già nell’altoforno si possono generare le condizioni di quasi completa desolforazione del bagno, per la quale si richiede un ambiente basico. Supponendo che lo zolfo sia presente nel bagno sotto forma di FeS (solfuro ferroso), gli studi sperimentali hanno permesso di rilevare il ruolo chimico svolto nella desolforazione da Mn (elemento presente nella parte più calda dell’altoforno), corrispondente al seguente:
FeS + Mn → Fe + MnS
Nell’altoforno l’ambiente è riducente e basico per la presenza di CaO usato come fondente, pertanto si ha:
MnS + CaO + C → Mn + CaS + CO
Queste reazioni si giustificano dall’analisi del diagramma di Ellingham (si ricorda che si tratta di un diagramma che mette in relazione l’energia libera e la temperatura delle reazioni di formazione di composti a partire dagli elementi, relativo alla stabilità dei solfuri: CaS (solfuro di calcio) è più stabile di MnS (solfuro di manganese) che è più stabile di FeS, per cui le reazioni di scambio che richiedono un ambiente basico e una atmosfera riducente sono possibili. Perché si ha la desolforazione? Dato che bagno e scoria sono due liquidi immiscibili, vale il concetto di “equilibrio di ripartizione”, secondo cui se una sostanza è solubile in entrambi i liquidi questa si ripartisce in essi secondo un rapporto costante a temperatura costante. FeS e MnS sono molto solubili nel bagno e poco nella scoria e tenderebbero a rimanere nel bagno; fortunatamente CaS è praticamente insolubile nel bagno, e passa integralmente nella scoria producendo la desolforazione. In realtà la desolforazione non risulta completa, e il modo per completarla consiste nell’addizionare al bagno spillato dall’altoforno Na2CO3, desolforante molto potente, che attiva le reazioni:
Na2CO3 → Na2O + CO2
FeS + Na2O → Na2S + FeO
e) Sul risultato della siderurgia in altoforno un ruolo fondamentale è svolto dalla affinità fra ferro e carbonio. Premettendo che le informazioni seguenti avrebbero bisogno precise giustificazioni (che esistono e sono il risultato di sperimentazioni eseguite da esimi metallurgisti partendo dal XVIII sec., continuate per tutto l’800, concluse soltanto nella prima metà del 900), si sa che in fase solida il carbonio può disciogliersi nel ferro in quantità dipendenti dalla temperatura e dal reticolo cristallino del solvente. Inoltre si possono formare carburi, di cui il più importante ha formula Fe3C ed è chiamato “cementite”. Si ammette che in fase liquida ferro e carbonio siano tra loro solubili in ogni proporzione. Quanto sopra, visto nell’ottica della operazione siderurgica in altoforno, ha la seguente conseguenza.
Finché la temperatura è bassa (circa 1000–1100 °C) e non permette la fusione completa della carica, la carburazione è assai limitata sia per la bassa disponibilità di Fe metallico (infatti a questo livello termico la riduzione degli ossidi di Fe arriva a FeO la cui riduzione a Fe è assai lenta) sia, e soprattutto, per la bassa cinetica del fenomeno di dissoluzione del C in Fe ancora solido. A temperature più elevate si ha la fusione della carica (attivata anche dal CaO che svolge la funzione di fondente), completa riduzione degli ossidi a Fe metallico e quindi la soluzione di C nella fase liquida. Modificando le modalità di funzionamento dell’altoforno si può regolare la quantità di C disciolto fra 3 e 5 % in peso, tenore che si ritrova nel prodotto finale anche dopo solidificazione.
Pertanto, a parte la possibile presenza di tracce di altri elementi chimici, si può affermare che il prodotto della riduzione degli ossidi di ferro nell’altoforno è un bagno costituito da ferro, carbonio, silicio, manganese, fosforo e pochissimo zolfo. Tale prodotto, una volta solidificato, si chiama “ghisa di prima fusione”: non è acciaio! E dell’acciaio non ha le tipiche caratteristiche tecniche e meccaniche. Ma ne ha di sue, talora tecnicamente molto importanti. Ci si limita a ricordare la più importante: allo stato liquido la ghisa è dotata di elevata colabilità, proprietà che ne fa un metallo adatto per impieghi in fonderia. Senza richiamare i suoi impieghi nel campo delle costruzioni meccaniche, la ghisa è molto usata nell’arredo urbano, dove le forme possono essere anche molto complicate.